|
 |
|
|
 |
|
|
 |
|
|
|
|
Rotary
joints:
A traditional joint might employ some rolling
or sliding interaction between the two connected links in
the form of a hinge or bearing assembly. The flexonic counterpart
moves by deflection, where elastic energy storage provides
an increasing resistance to rotation. Other issues when designing
flexonic joints include range of motion, axis-drift, off-axis
stiffness, and stress concentrations. We have identified several
joint designs for possible inclusion within flexonic mechanisms.
Below is a simple thin-strip cross-flexure joint. The right
graphic depicts a cross-flexure joint in its rotated configuration.
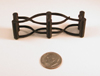 |
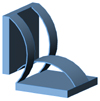 |
A rotary joint can also be designed by utilizing the twisting
degree of freedom of a thin strip. A realization of this joint
is proposed and analyzed in detail by Moon, et al [1]. The
joint utilizes perpendicular ribs along the flexure region
to constrain off-axis motion. The ribs are essentially the
intersection of two perpendicular thin strips. The axis of
rotation is along the center of the ribbed flexure.
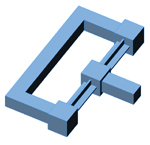
back
[1] Moon, Y.-M., Trease, B. P., and
Kota, S., "Design of Large Displacement Compliant Joints",DETC2002/MECH-34207,
ASME/DETC 27th Biennial Mechanisms and Robotics Conference,
Montreal, CANADA, Sep.29~Oct.3, 2002
|
|
|
 |
|
|
|
|