|
|
Flexonics
are radically different from traditional electromechanical
systems in both form and manner of construction. The
term "flexonics" derives from the fact that the
proposed mechatronic systems achieve motion through flexion
(bending). There will be no traditional sliding or rolling
movements in actuators, sensors, or joints. Thus, flexonic
devices will not utilize or need gears, bearings, or any sliding
surface. Motion and force will not be gererated by motors,
but by the expansion and contraction of dielectric elastomer
actuators. Because of this design strategy, there are no discontinuities
between mechanical elements within a device. Therefore, a
flexonic device can be constructed as a single part, without
post-processing.
Flexonic devices will be fabricated using an inkjet printing
technique. Through selective material deposition, a mechanism
can be built layer by layer with a high level of complexity
and integration. A necessary component of inkjet polymer
printing will be a diverse set of printable materials.
These include solution-based polymers and oligomers, nanoparticle
suspensions, and other polymers that flow when heated.
The range of current polymer-oligomer-nanoparticle capabilities
includes electro-mechanical sensing and actuation, specialized
structural support, and electrical conduction. Our goal
is to utilize this diversity to construct both active and
passive mechanical components. Ultimately, we intend to integrate
driver and control electronics using the technologies being
developed by Prof. Vivek Subramanian and his Organic
Electronics Group.
Flexonic devices are not intended to replace all traditional
mechanical systems. However, flexonic manufacturing and design
offer a unique set of properties suitable for a variety of
applications. Like most printing processes, there is no "charge"
for complexity, only for the volume of material. Printing
techniques allow high-complexity designs at low cost, so low
that massive redundancy can be used to increase reliability
as much as is needed. By exploiting the benefits of a diverse
set of polymers, mechatronic devices can be made lightweight, with high
energy densitites and efficiencies. Structural material properties can
be soft and rubbery to hard and rigid. Applications range
from the mundane (shape-changing furniture) to the exotic
(anthropomorphic robots).
|
|
|
 |
|
|
|
simple
gripper demonstration one-piece construction and flexible
finger mechanism
|
|
piezo
printheads from MicroFab, Inc.
|
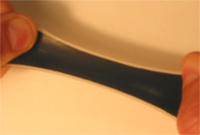 |
polymer
actuator material |
|